CAL
—
Volumetric 3D Printing
Student - Fall 2020 to Spring 2021
My master’s capstone project expanded upon the 3D Volumetric Printing called CAL developed by Professor Hayden Taylor. CAL projects images onto a rotating vat of resin to cure the resin into a 3D print. This system has the potential to bring 3D printing to mass manufacturing, as it drastically decreases the time needed to 3D print objects.
The current mechanism is small for manufacturing standards, so I developed a way to scale up this mechanism.
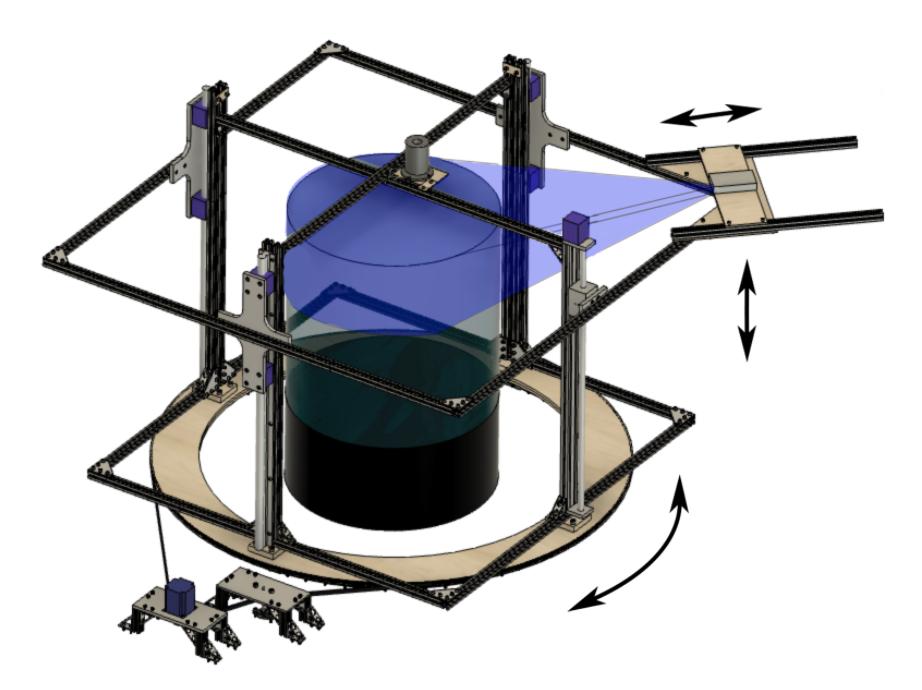

Previously, the resin container rotated while the projector remained stationary. The hindrance for simply enlarging the original design is that the curing process cannot begin until the resin in the container has reached the same angular speed. The time needed to do so increases with an increase in container size.

I proceeded with a mechanism that rotates the projector around a stationary vat in order to overcome the time increase from enlarging the current CAL design to print larger objects. Therefore, the vat of resin never moves, and the mechanism no longer needs to wait to start projecting for the resin to settle into rotating at a constant angular momentum.
To rotate the mechanism, A large belt pulley sprocket is attached to the circular track, and the sprocket is then circled by a belt. To ensure the belt would not slip off of the sprocket, the sprocket was made of two halves with an outer lip that bolted together. The belt is driven by a motor, and a tensioner is included to ensure the belt does not have any slack.
To rotate the mechanism, A large belt pulley sprocket is attached to the circular track, and the sprocket is then circled by a belt. To ensure the belt would not slip off of the sprocket, the sprocket was made of two halves with an outer lip that bolted together. The belt is driven by a motor, and a tensioner is included to ensure the belt does not have any slack.

A rack frame lies on top of the sprocket to carry and move the projector vertically, as it projected onto the larger vat of resin. The vertical movement is made possible by a vertical linear actuator and three vertical undriven linear rails. T-slot extrusions were used as support as a lightweight and easy-to-assemble option for the structure of the rack frame. Brackets were used to connect the extrusions together and to other components in the mechanism assembly.
The projector’s distance away from the container can also be adjusted to allow this mechanism to be used with different sizes of vats. Currently a user is able to change this distance by-hand, yet the design of this component will need to be changed to ensure defined locations limit the distance between the projector and the center of the container. This way, it will provide the user with a simple and precise way to change the configuration of the mechanism for a change in size of the container.

This design was finalized and the parts to assemble this design were ordered. The labeled motor system may be modified, as it is dependent on the successful implementation of the in-house manufactured large sprocket. Once the enlarged CAL mechanism has been built, the quality of the resulting prints will then be compared to those made with the previous smaller mechanism. Additionally, it would be possible to obtain the amount of time necessary to print a multitude of copies and determine if this lies within an acceptable range as determined by mass manufacturing standards.
It was not possible to assemble and test the mechanism, as the project was completed entirely online due to safety precautions taken to reduce the spread of COVID-19.
It was not possible to assemble and test the mechanism, as the project was completed entirely online due to safety precautions taken to reduce the spread of COVID-19.
